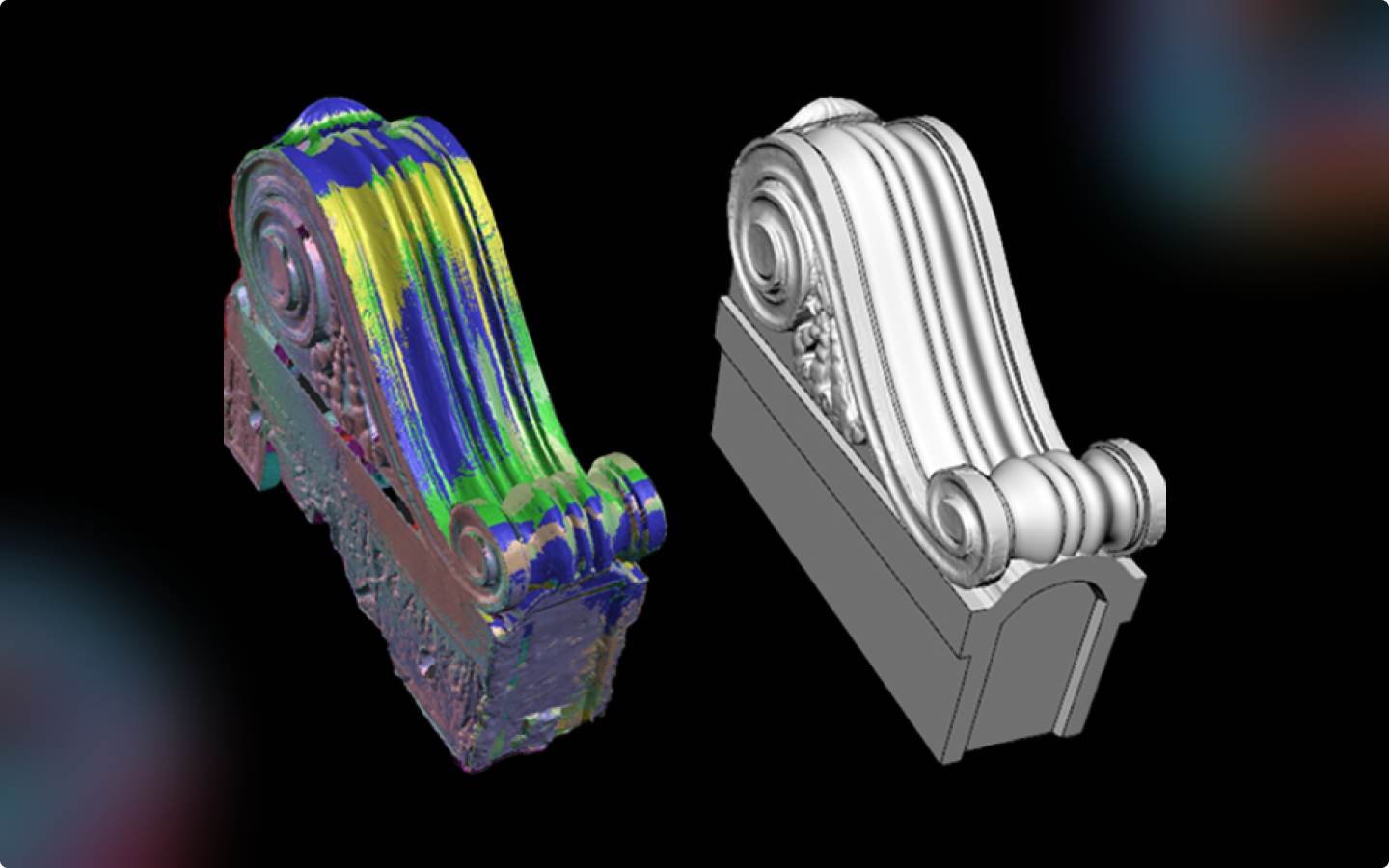
What was the central goal?
When I joined Boston Valley in 2015, the company was in the midst of a major transformation of both its design and prouduction pipelines. By leveraging emergent technologies, the company could gather site data (photogrammetry and point clouds), produce 3D models (Rhino, Grasshopper, and Python), and build terra cotta blocks (CNC molding and foam cutting) more effectively and more accurately. The company found a willing partner in the University at Buffalo, as advanced computational design was a core part of our architectural curriculum.
My role included using profile measurement tools and laser cutters to accurately measure and model complex terra cotta samples.
In addition, I also:
(1) built intricate, watertight 3D models using Rhino and Grasshopper,
(2) wrote and edited scripts in Python to expedite manufacturing processes and
(3) designed façade assemblies to propose structural elements.
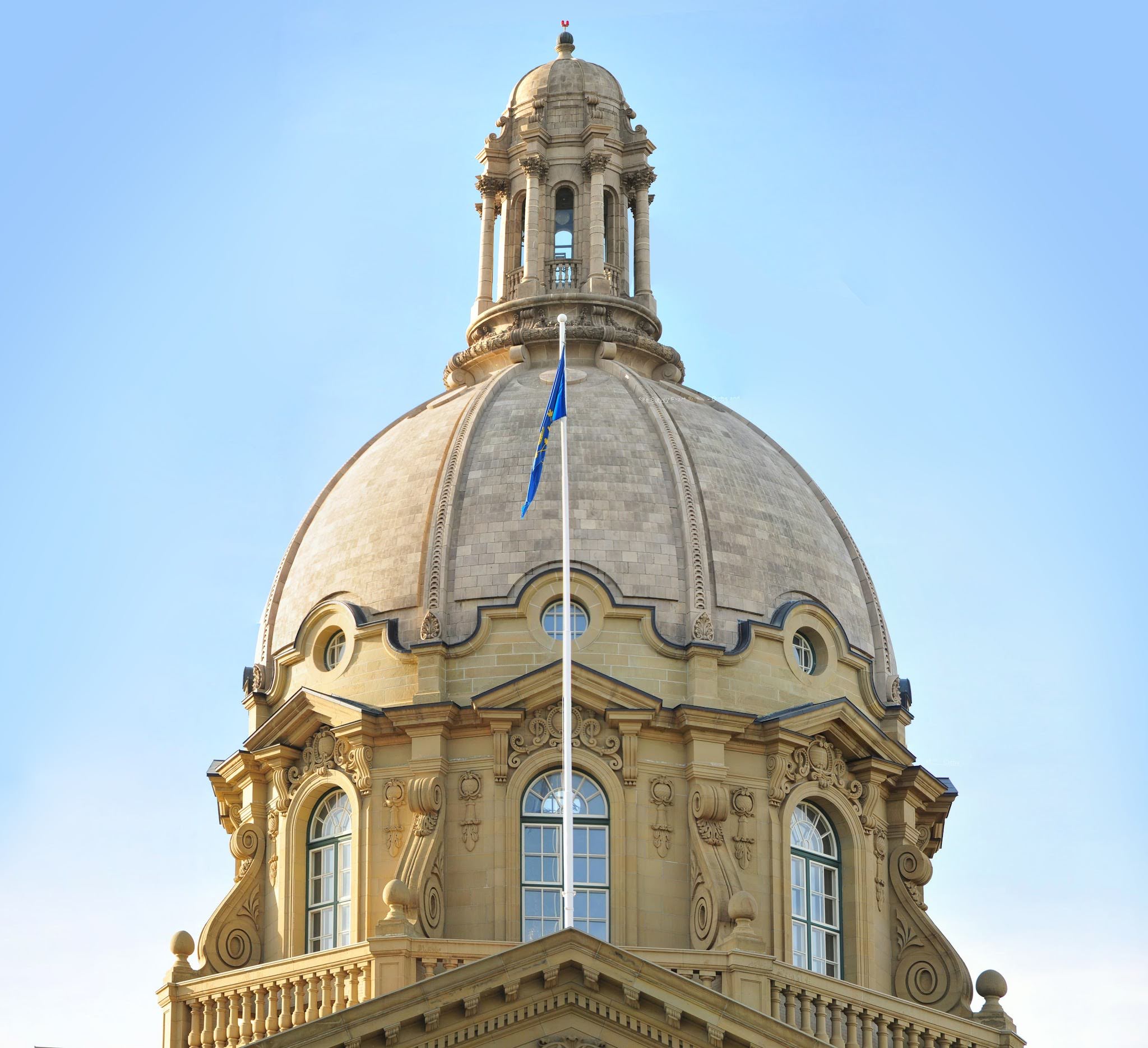
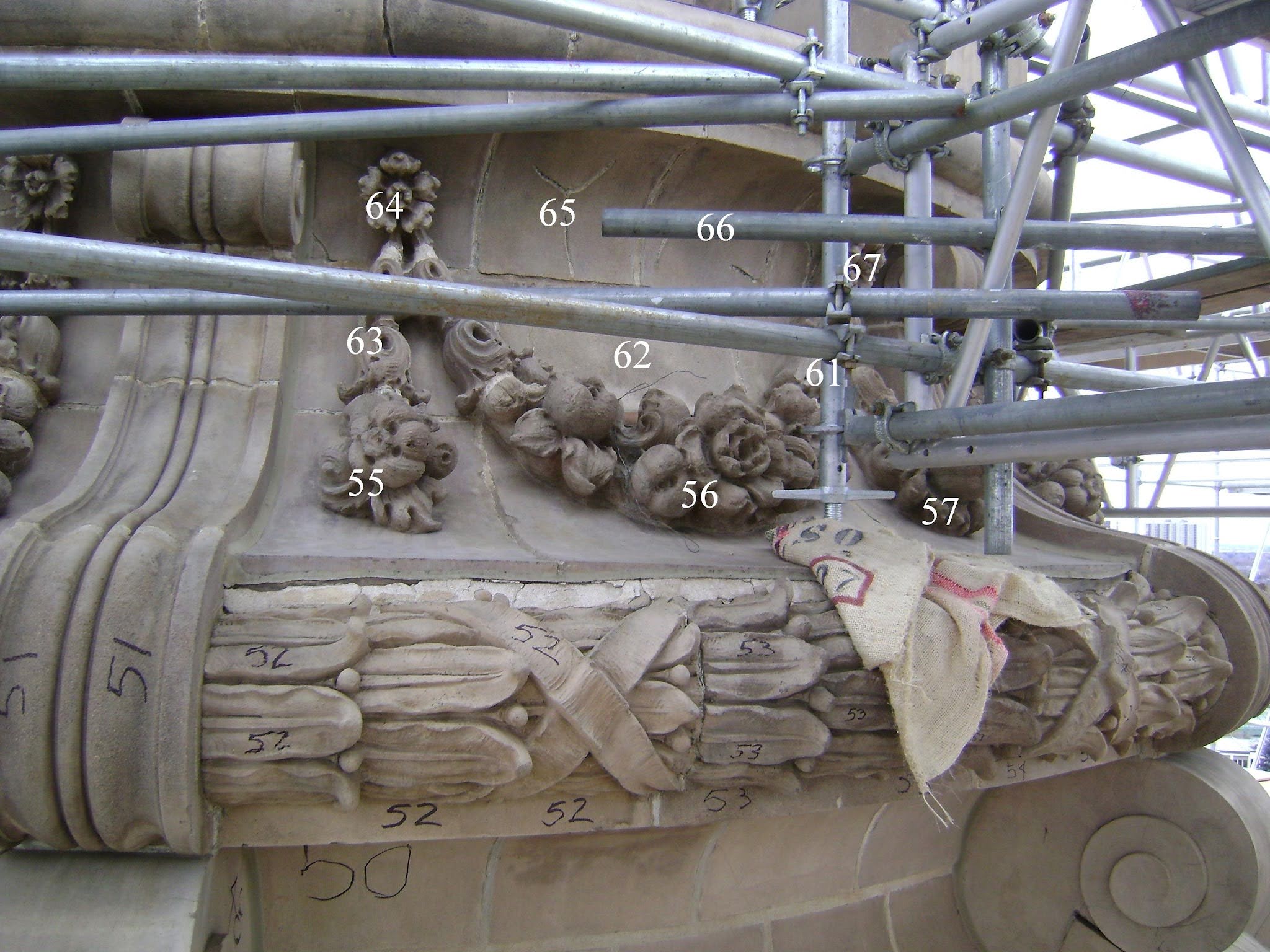
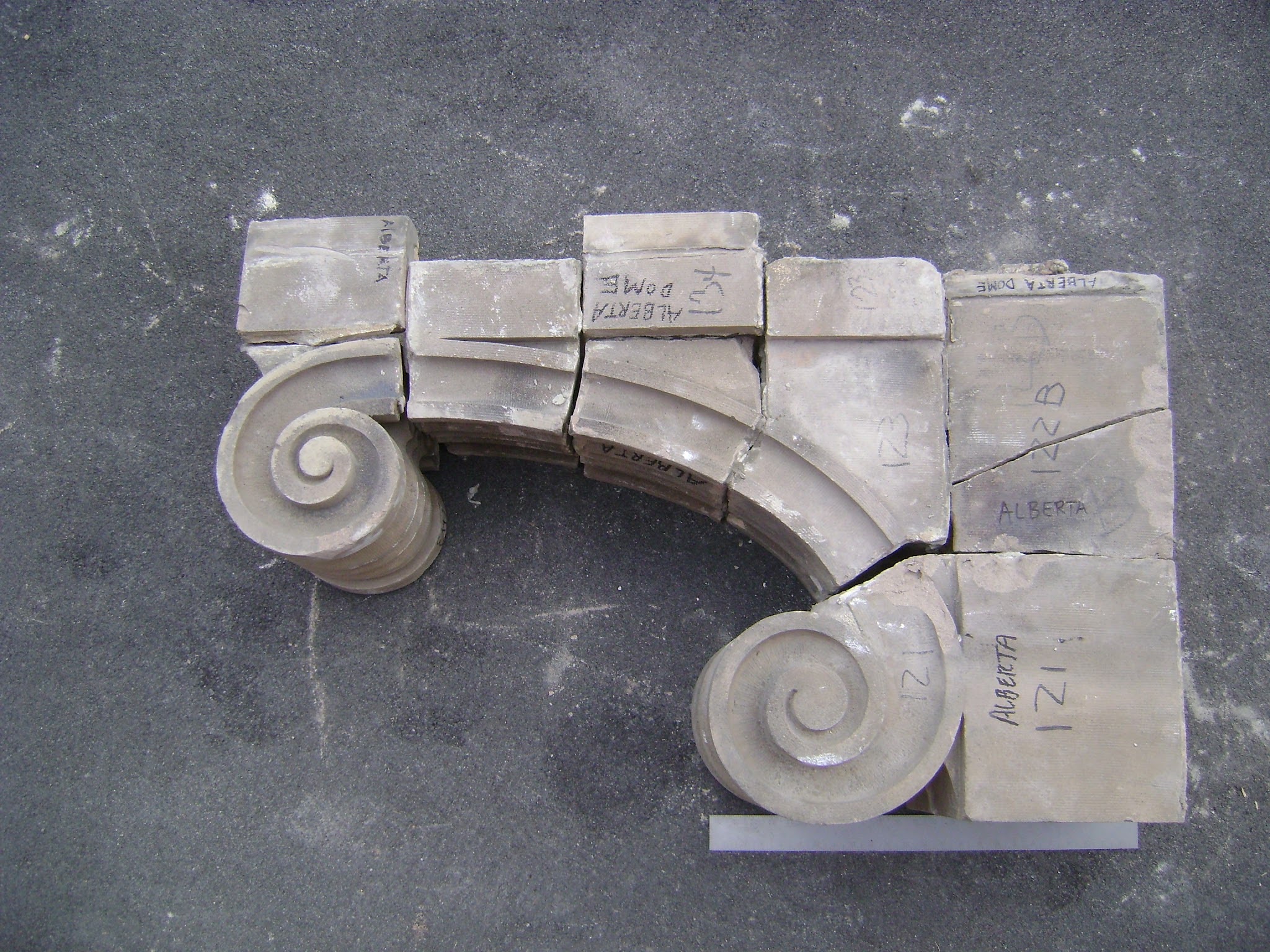
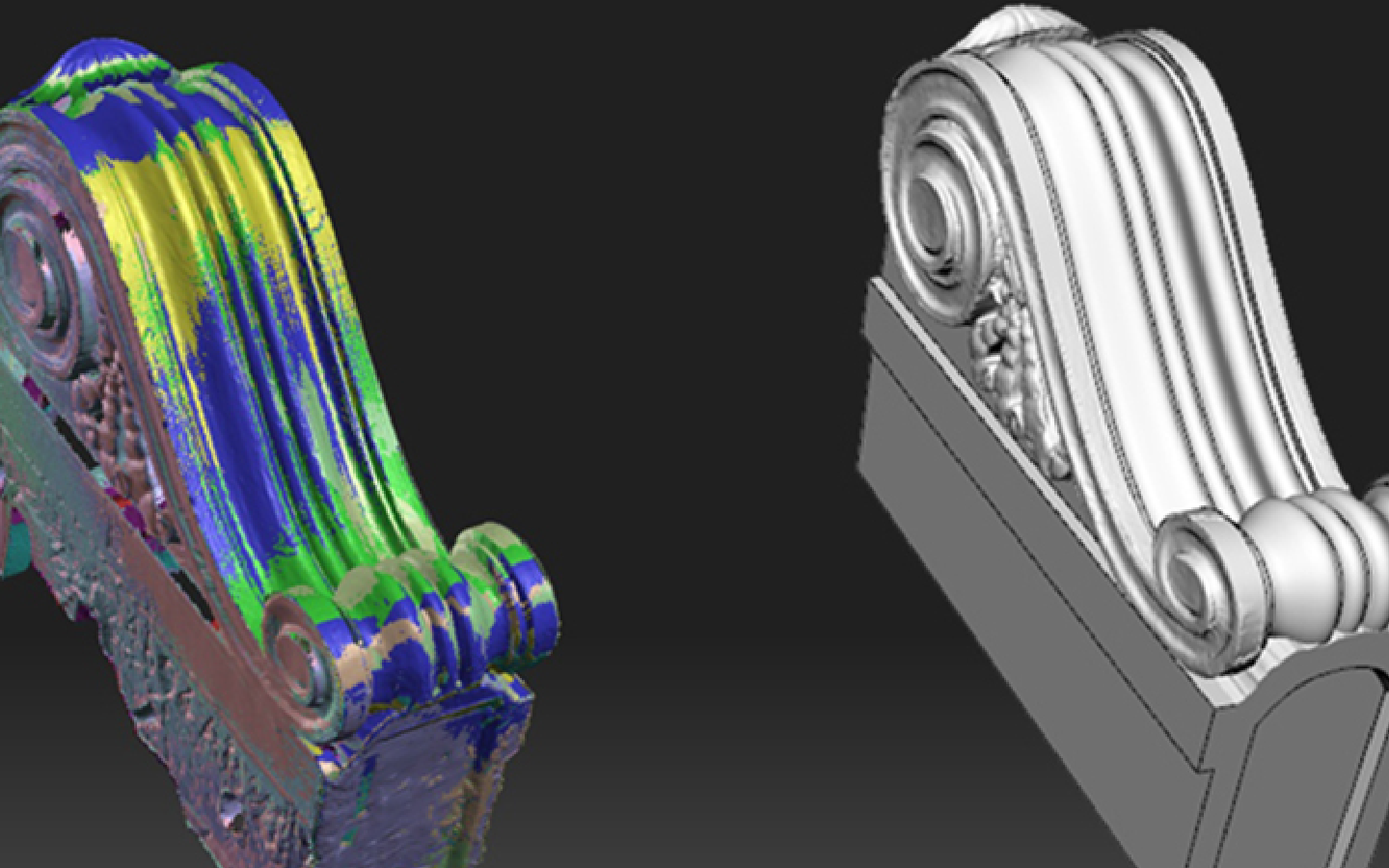
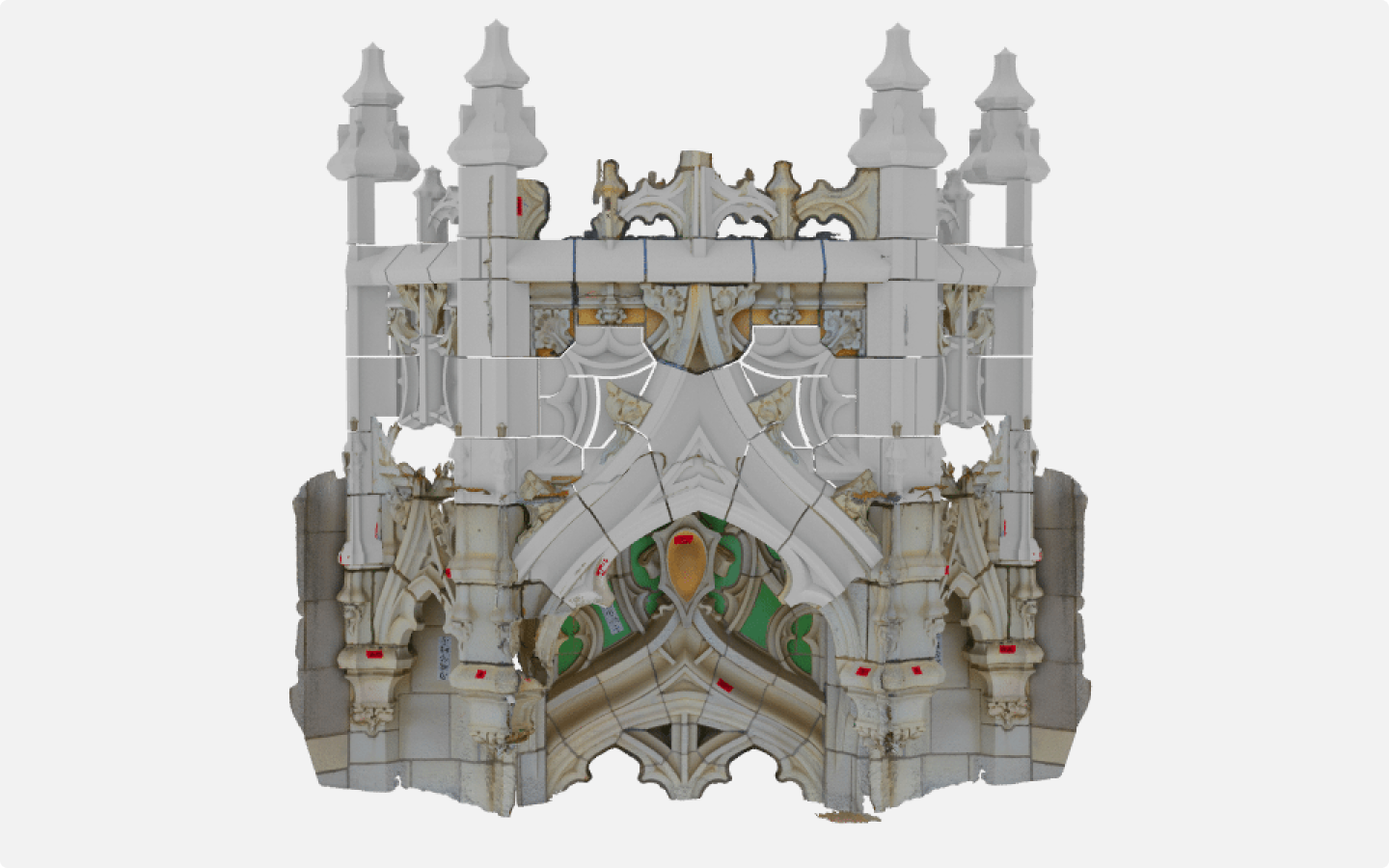
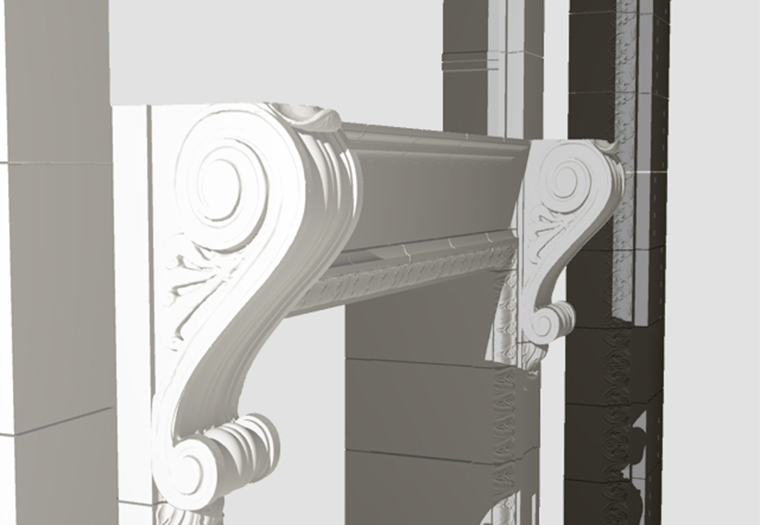
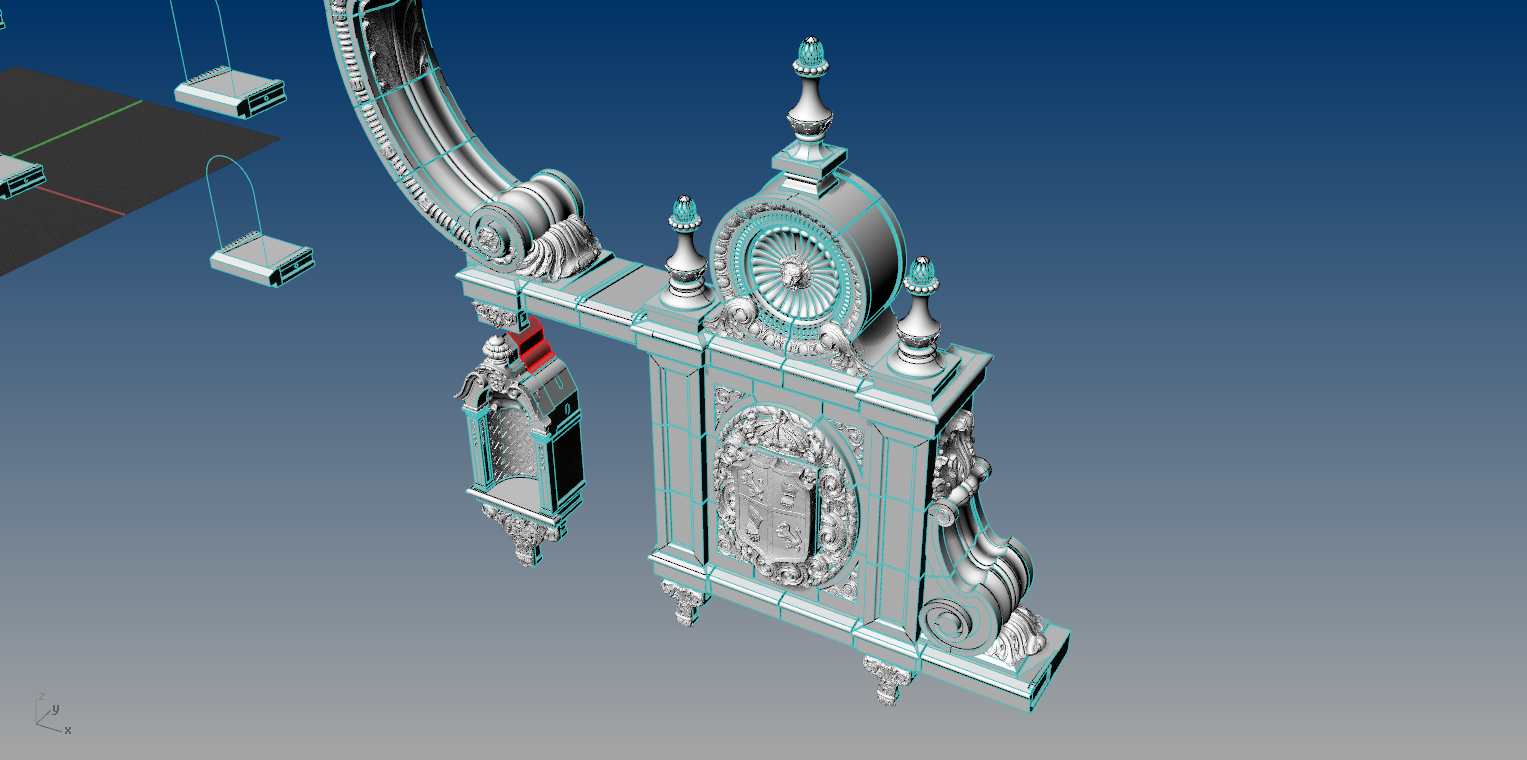
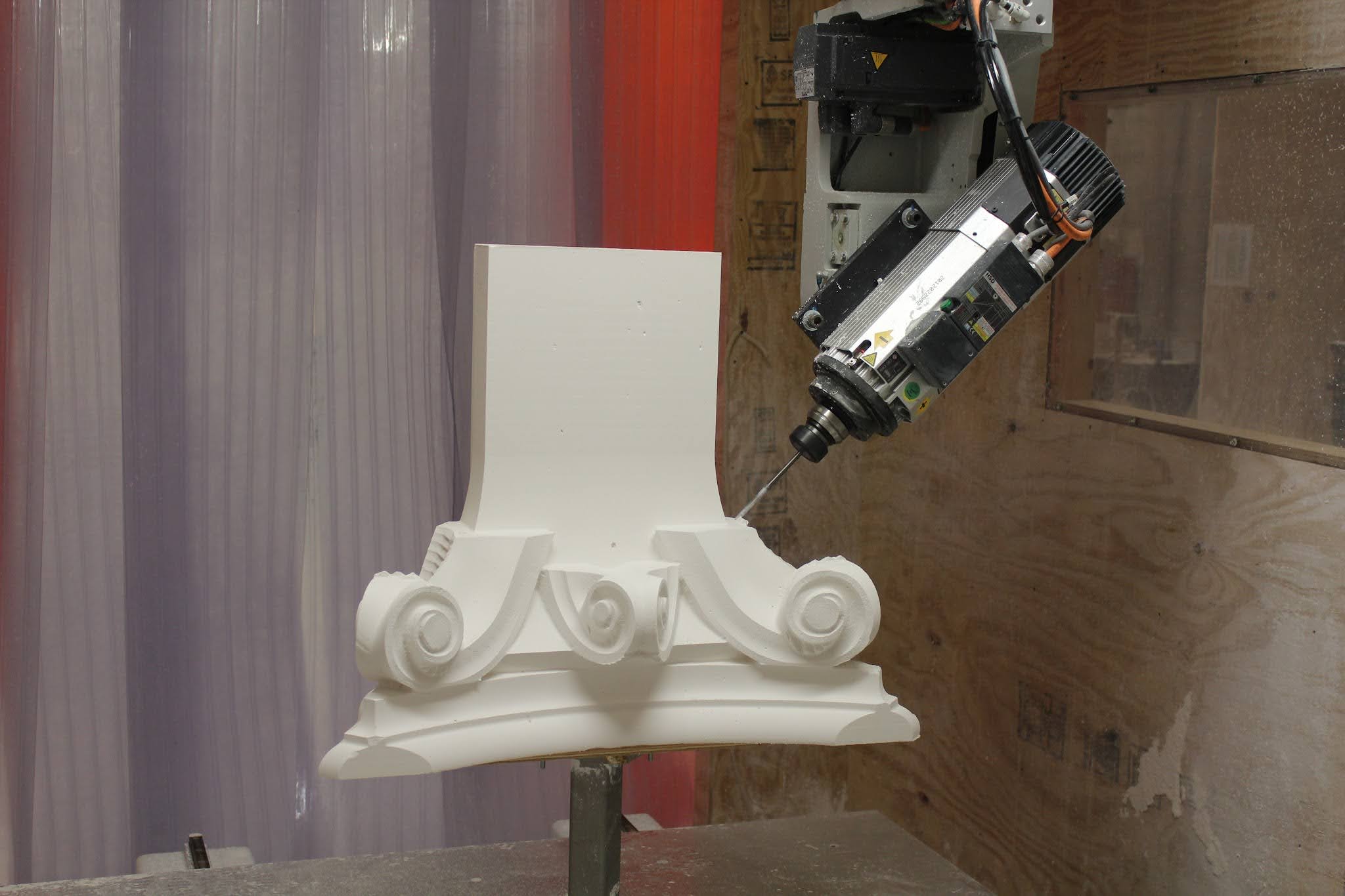
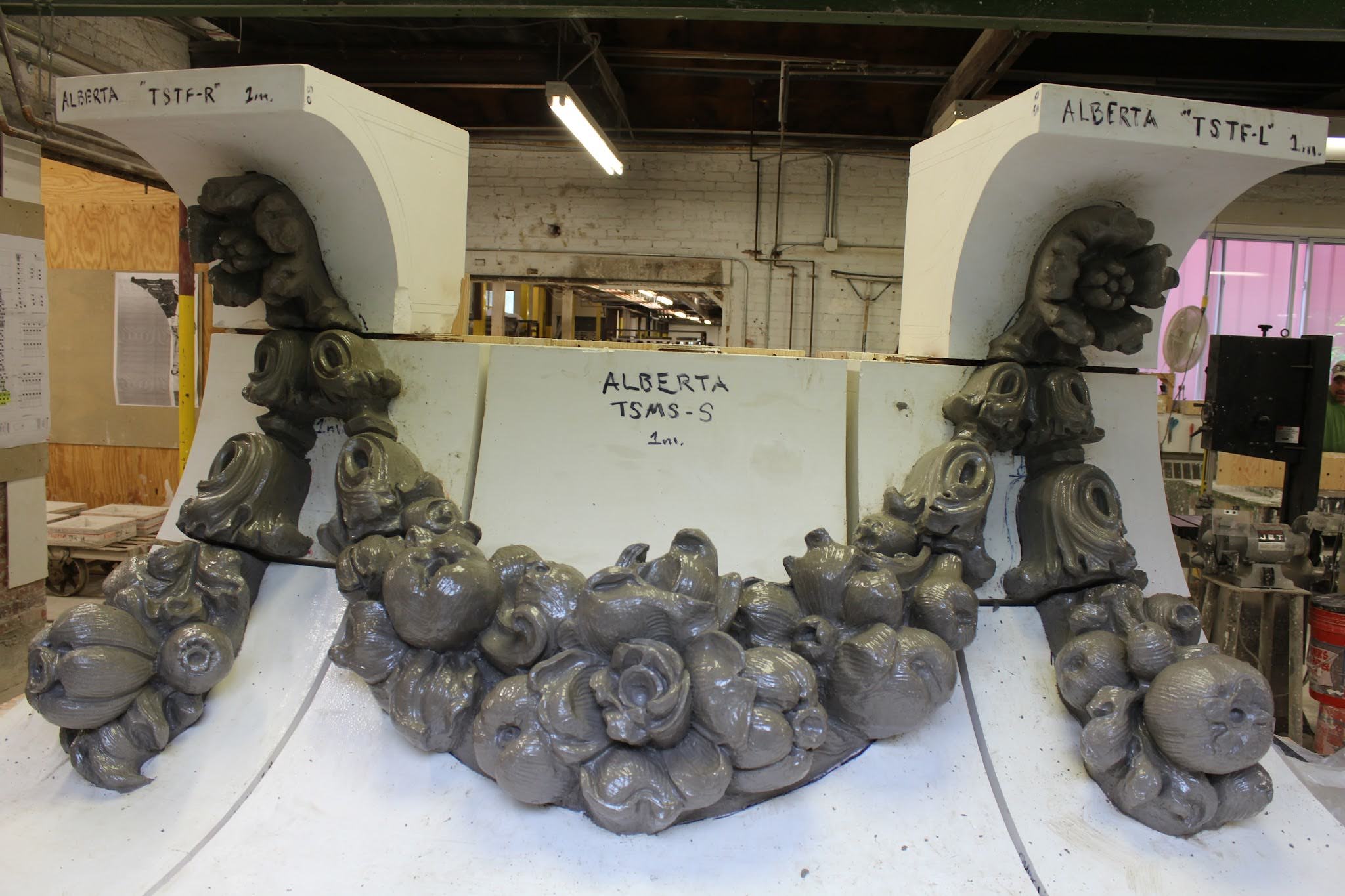
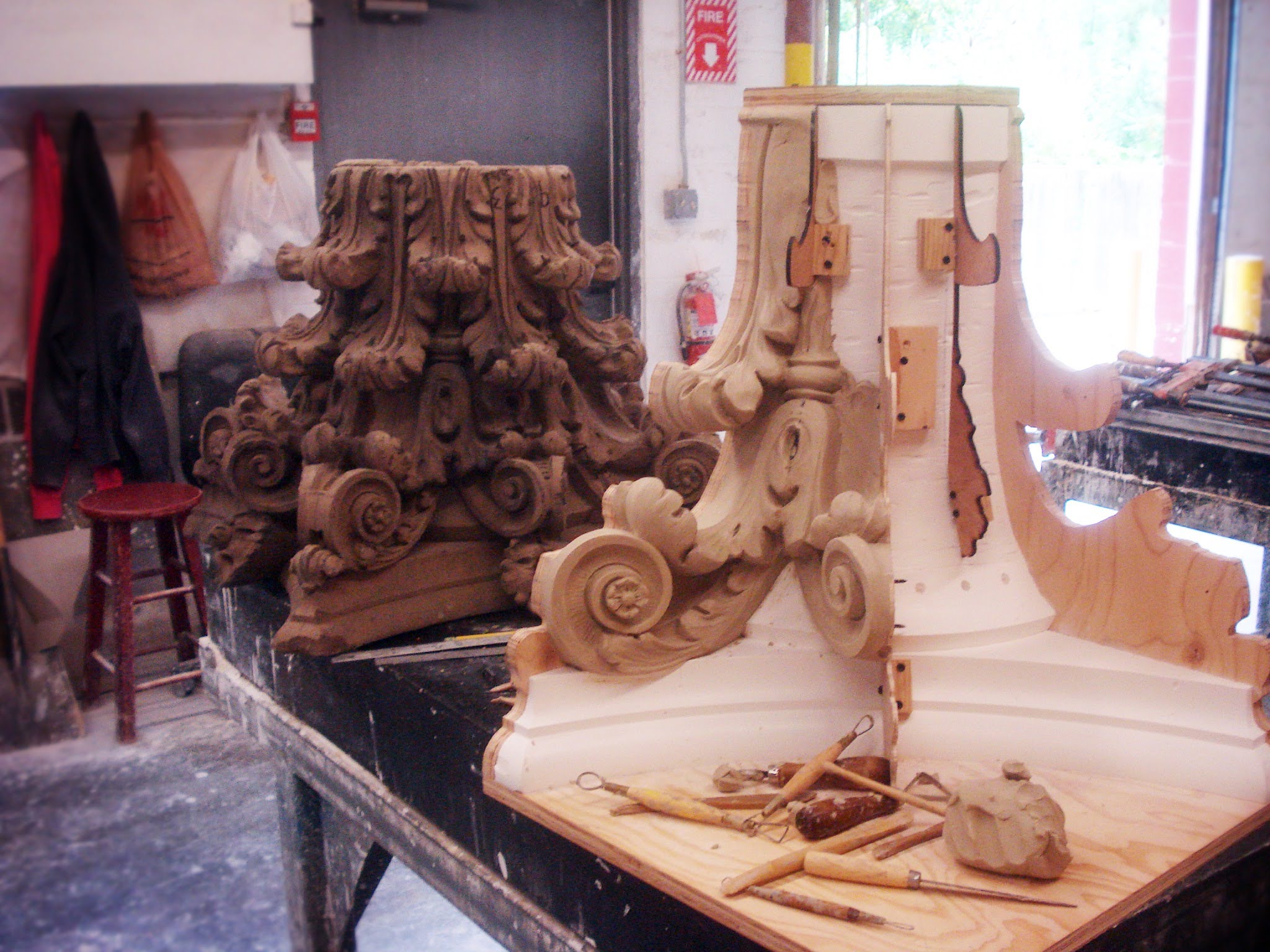
And the tl;dr
Projects at Boston Valley were detailed, nuanced, and fascinating. Here are a few things I'm proud of about my time there.
- I begged to rotate between all of the departments. This helped me to understand the entire workflow – from when samples are delivered to when the final blocks are shipped out. Not only was I picking up new Rhino and Python skills everyday, I also learned how to make molds, do advanced CNC work, work a kiln, and pack finished blocks for safe delivery. It is an honor to learn alongside tradespeople and see them at work.
- I got swole. My car was an old beater that drained my bank account. So I biked from downtown Buffalo to BVCT at least three times a week. That's 50 miles a day. And then, once I got to work, I was carrying around 60lb stones all day! I was a beast. I channeled the physical strength to complete a century in the Ride for Roswell, raising money for cancer research.
- I learned to back up my work. When a huge layoff hit our department, I was let go. Sadly, there was no time to document the gorgeous work I'd helped create. Now, I rigorously document as much as I can. While we're on the topic, all images on this page are from Boston Valley. They're projects I worked on, but I do not own the images.

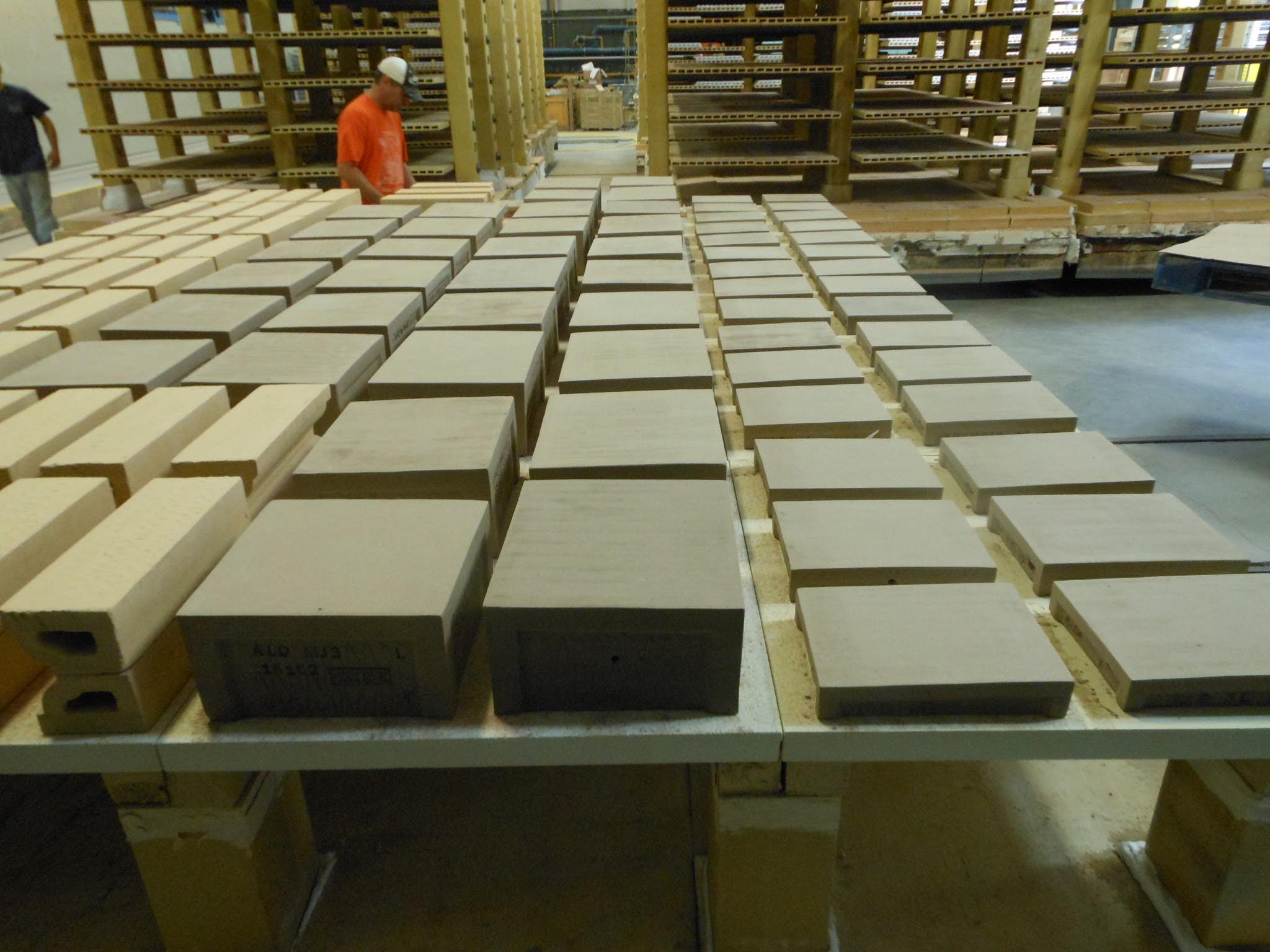
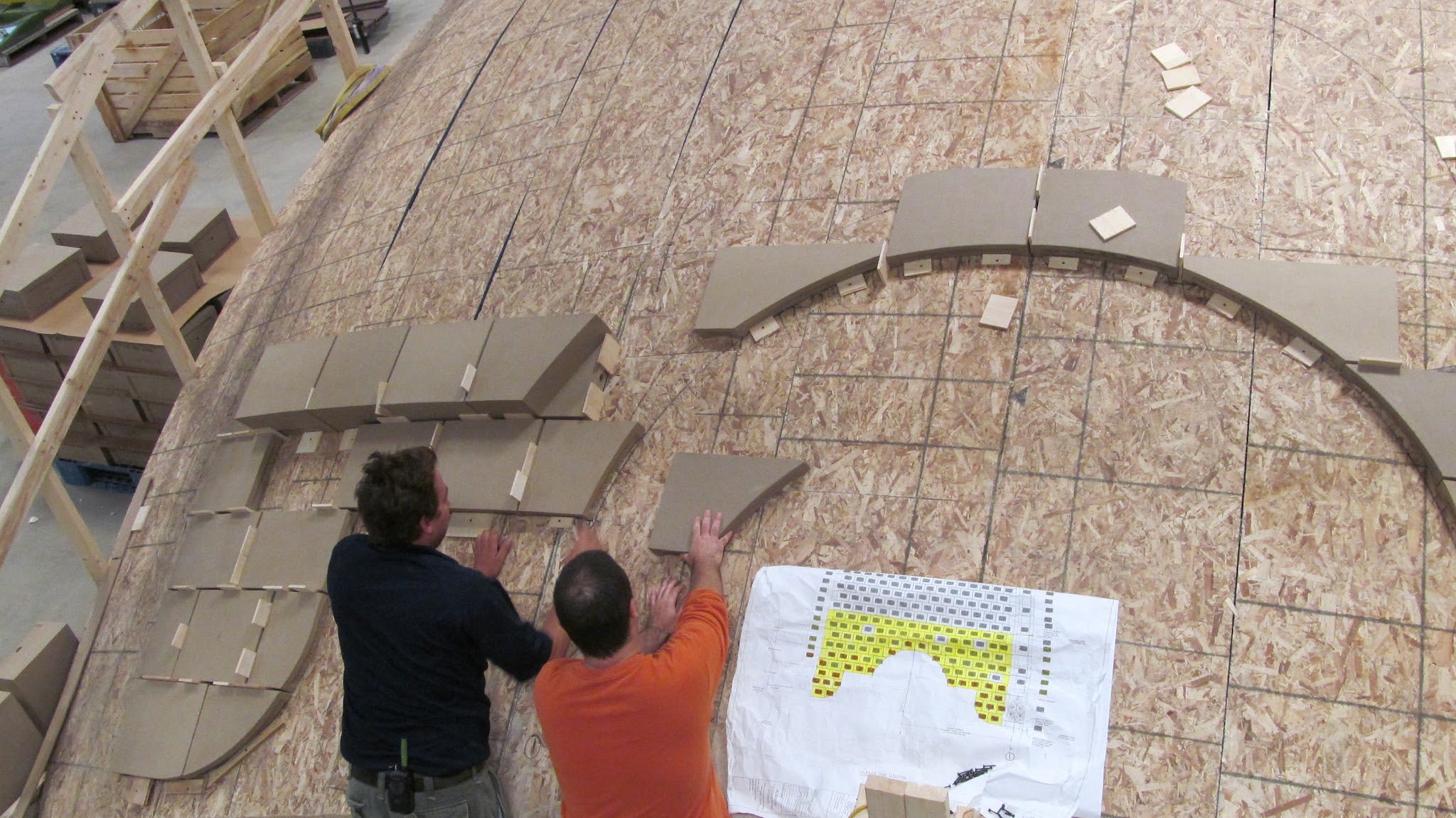
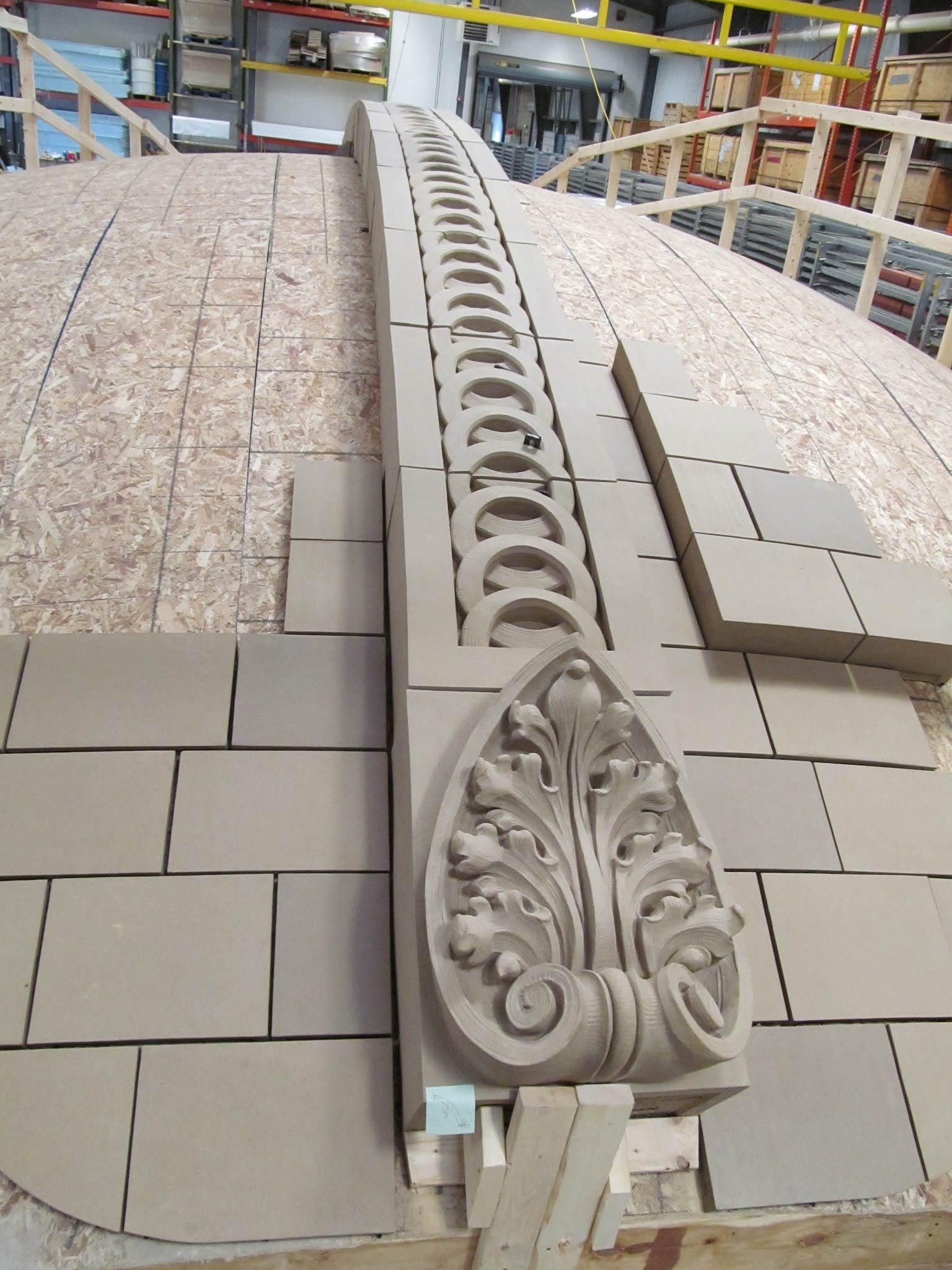
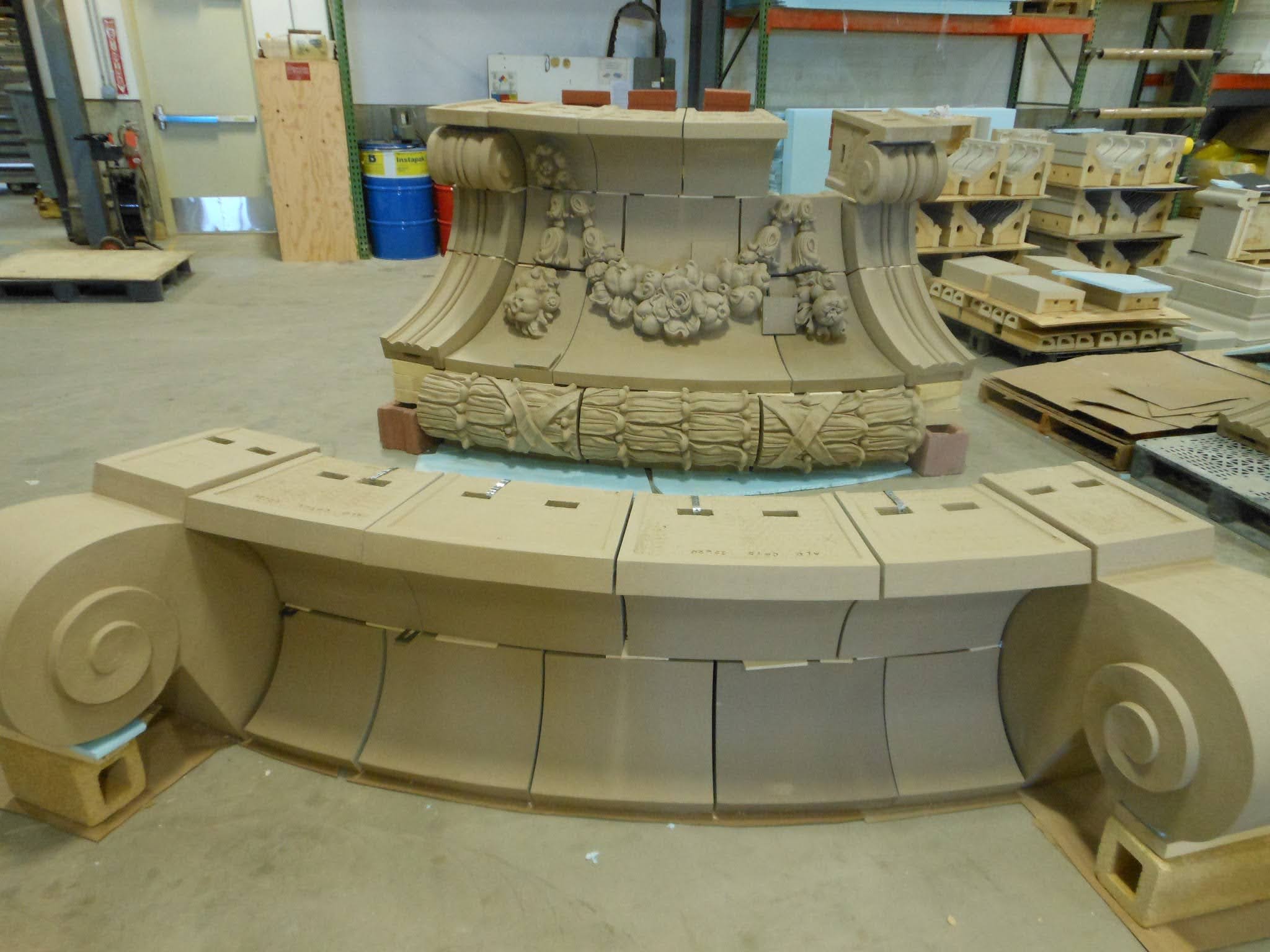
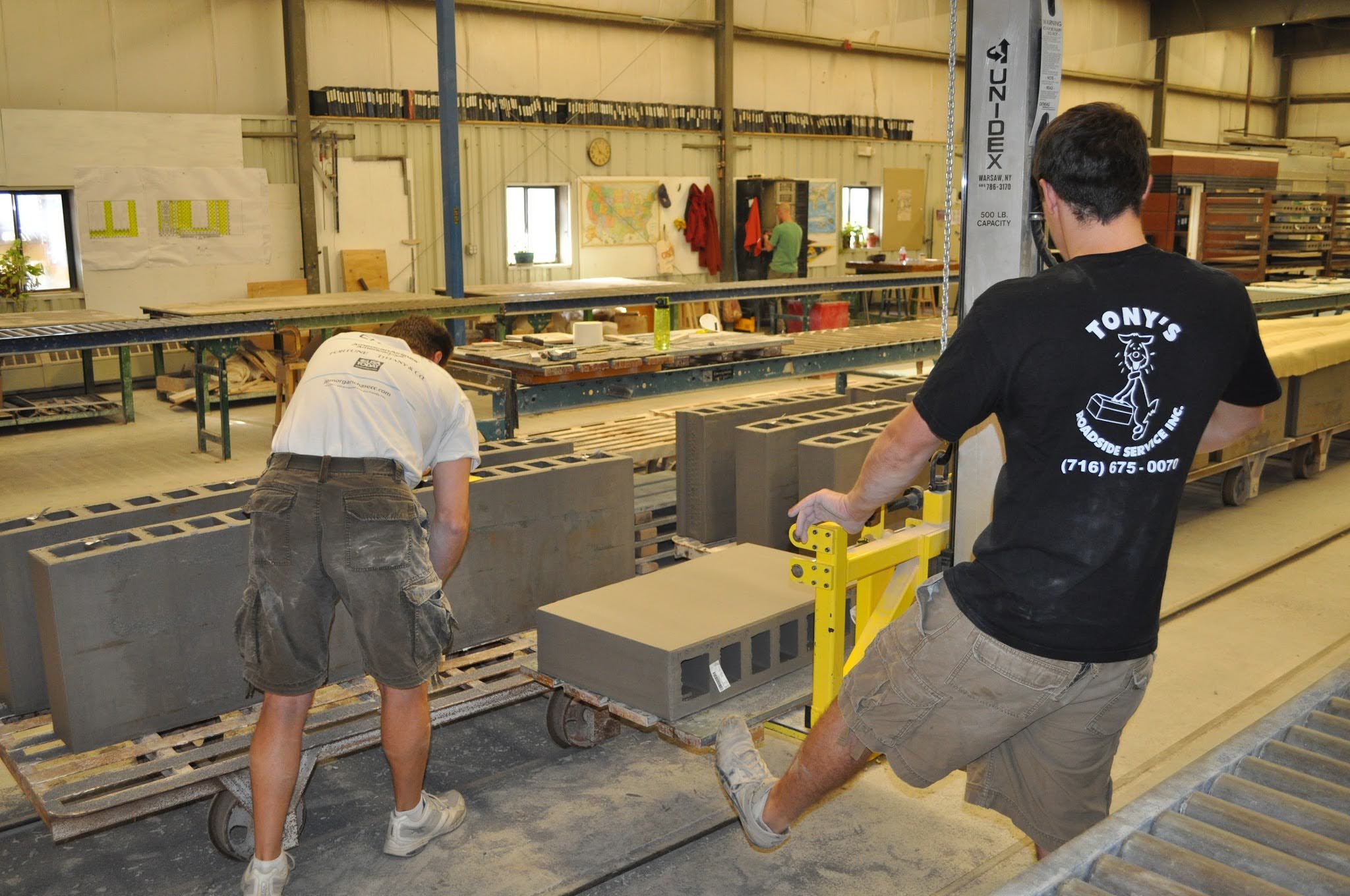